How to use additive manufacturing in the defence industry
The defence industry is using additive manufacturing not just for the supply of spare parts, but also to produce new and vital components.
Considerable experience with large-scale AM
“In a recent project we showed that we can manage these challenges”, says Michel Honoré, Project Manager at FORCE Technology. In his presentation ‘Moving from CNC to AM’, Michel compares cost and lead-time of an additive-manufactured part for the Joint Strike Fighter with the CNC-machined equivalent.
Our experience within metal additive manufacturing is quite extensive, and in recent years, we have focused mainly on large-scale AM. “With a robot and a multi kW laser source, we can manufacture big parts, up to 3 meters in length and 1 metric ton weight, at our facility in Lindø”, Michel Honoré explains.
For producing these kinds of applications, we apply a self-developed laser metal deposition system with wire and an industry-standard DED unit that uses powder.
Manufacturing F35 part with AM and CNC machining
"For manufacturing companies in the defence industry, additive manufacturing is a useful technology", Michel Honoré says.
Besides for rebuilding worn-out parts or building replacement parts for the ageing jet fighters of the Danish air force, there are also benefits of using AM for manufacturing new parts. We have recently developed a real application for the F-35 Joint Strike Fighter.
“If we compare traditional manufacturing - CNC machining - of this type of parts with additive manufacturing, AM has a lot of benefits, even though there are also challenges”, Michel Honoré says. He has a background as an engineer in welding.
Overcome the challenges of a welding process
“An AM part is a 100 per cent welded part. In aerospace applications, you want to minimise everything that has to do with welding, because of the defects the welding process can introduce. So this challenge should not be underestimated”, Michel Honoré says.In the mentioned project, we showed that it is possible to overcome the welding problems and control the process to deliver good parts. So, with the right approach, you can use laser metal deposition for building new parts for jet fighters. And by applying additive manufacturing, there are benefits in both time and money. Especially the latter.
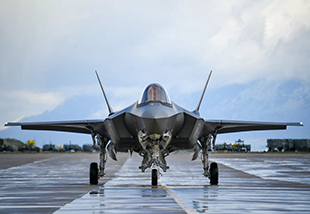
Case