Let CFD do the trim optimization for you!
Trim optimization is one of the easiest and cheapest methods for ship performance optimization and fuel
consumption reduction. It does not require any hull shape modification or engine upgrade. The optimum trim can be achieved by ballasting or by choice of loading condition.
Extensive optimization experience
Although trim optimization tests are considered less important than standard power performance model tests they can provide substantial savings and a return on investment between one and six months, depending on vessel type, operation and number of vessels in the series. The energy savings as a result of trim optimization have been proven in theory and praxis in many years of operation.
FORCE Technology has performed around 50 model trim tests within the last 10 years with savings up to 15% in propeller power at specific conditions and up to 3% in overall savings. Trim guidance to more than 400 ships has been provided in order to increase the operational efficiency and to reduce emissions and fuel costs.
Potential flow codes vs. RANS CFD
Due to improving CFD capabilities and computational resources, trim optimization can easily be executed using numerical simulation models. While simplified codes such as potential flow codes have been used in the past to estimate vessel performance and flow patterns, it is state of the art to use RANS CFD codes for that purpose.
In order to map the influence of trim, draughts and speed on the performance of the ship the turbulent flow features of the vessel will be analyzed with the high efficient RANS CFD code STAR CCM+. Since FORCE Technology has many references and validation data for model tests, the CFD simulations for the trim optimization will also be performed in model scale.
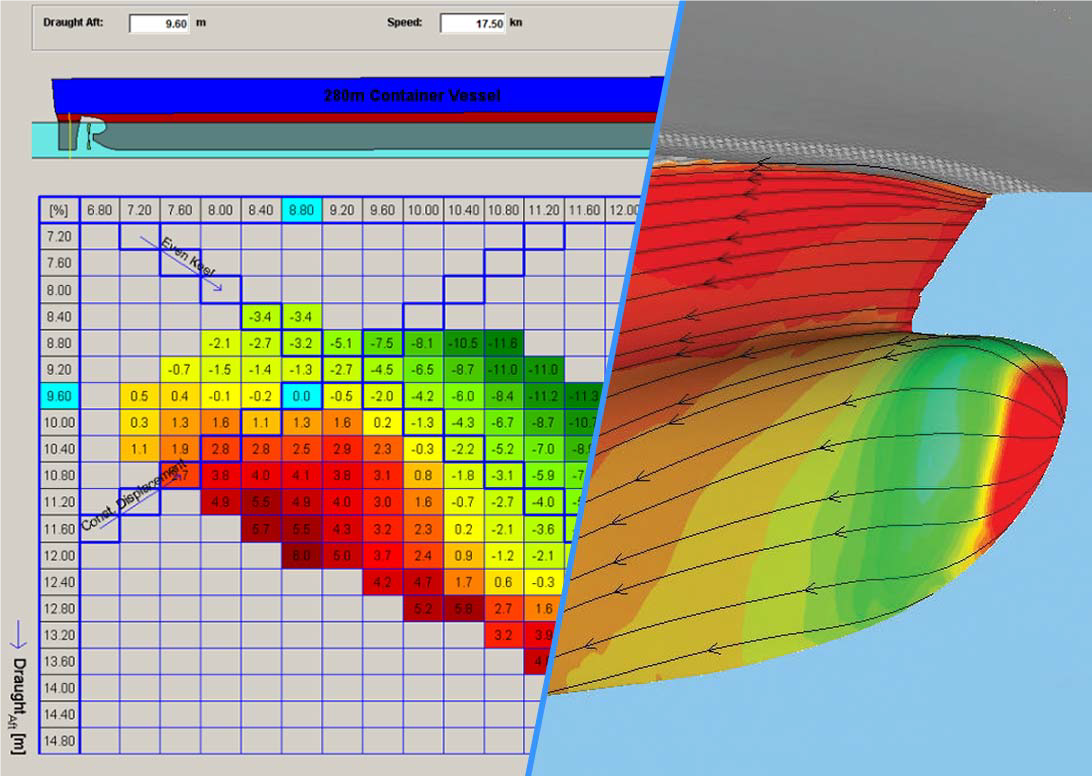
For a complete set of a standard trim optimization, a total number of resistance computations has to be chosen. Usually, a number of 120 - 180 conditions, which cover 3 to 8 draughts at each 3-7 trims and 4-6 speeds are chosen for the numerical towing tank tests. The conditions will be carefully selected to match the operational profile of the vessel.
Power demand optimization
To predict the propeller power demand, propeller open water and hull interaction data based on FORCEs inhouse database will be taken into account together with resistance data from CFD. We are currently working on the integration of our simplified body force propeller model in order to include the propeller effects directly in the RANS CFD simulations. Though, delivered power, hull efficiency, thrust deduction, relative rotative efficiency and the wake fraction, i.e. the average axial velocity over the propeller disk, can efficiently be estimated and compared to results of experimental model tests.Full-scale performance
Based on the results of the simulations in model scale and the predicted form factor from additional RANS simulations, we are able to predict the full-scale performance and the relative differences in propulsive power for the complete trim optimization matrix based on the propulsive data from our experimental model test database.All the output from the performance evaluation, including power prediction and relative power savings compared to the even keel condition can be used as basis for the trim guidance. FORCE Technology’s software SeaTrim handles the transaction of numerical performance prediction and trim guidance for the ship operation.
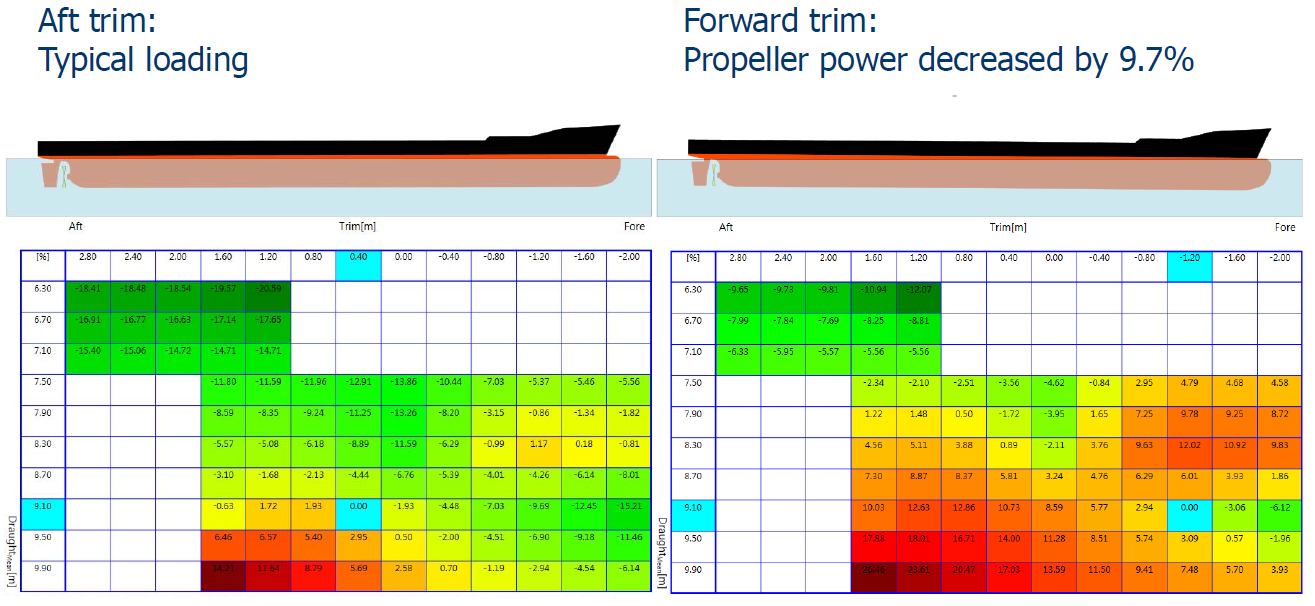
The optimal trim based on the optimal power demand of the vessel is not necessarily the trim optimal condition concerning ship stability, longitudinal strength, ship manoeuvrability or overall safety. The ship master should naturally evaluate the optimal overall operation.