Space propulsion, rocket nozzle design and manufacturing
Space technology spin-offs give your company high-tech competences that will benefit your overall performance.
Getting Europe into space
For two decades, we have participated in setting new standards for space propulsion, rocket nozzle design and manufacturing for the next-generation launchers. We are mainly working through assignment from ESA, the European Space Agency, and directly under their allied partners.
Our contribution has accomplished great success in the European space and aerospace industry. As a result, the nozzle design has been chosen for the new Ariane 6 rocket, which is expected to be launched 2019.
Working in the space business sets the toughest requirements on performance, quality and reliability. Our contribution focuses on development and manufacturing in metallic and composite materials, combining four of our key competences:
- sensor technology
- automation
- non-destructive testing (NDT)
- laser fusion and additive manufacturing.
Through our involvement in the European space business, we are literally participating in getting Europe into space.
Space technology spin-off and your business
Our innovation comes from working on one of the most difficult products in the world. We use space as a foundation for process and technology development and offer expertise concentrated on sensor technology, laser fusion, additive manufacturing and NDT all of which often applies in an automated context.
Integrating space technology can give your business high-tech competences and benefit your overall performance, e.g. reduce costs, enhance production or inspection speed.
If your project could benefit from these technologies, we are very interested in working with you. We offer to deliver in all steps from the development phases such as concept study, prove of concept, demonstration, delivery of equipment, turnkey systems, support, training and technology transfer.
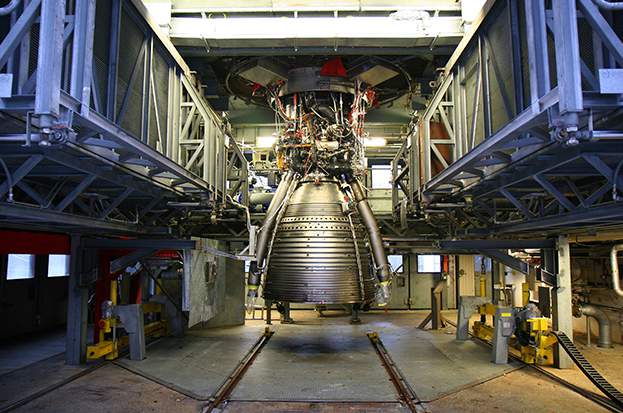
Designing the nozzle for the Ariane rocket
Our involvement in the space adventure began in 1996 with an objective set by the European Space Agency (ESA). ESA asked for a new nozzle concept in order to maintain their leading position in nozzles for rocket engines. The new design concept should be scalable to various engines, reduce production costs and shorten lead time without compromising reliability.
During the concept discussions, there was a unique opportunity to introduce new process technologies that would present a breakthrough in design never made possible before. Furthermore, improved process repeatability and robustness was achieved by introducing more machine-controlled processes in the manufacturing and quality control of nozzles.
Future involvement in the Ariane project
We are continuously involved in the evolution of the main engine of the Ariane rocket. The new Ariane rocket will be Ariane 6. The project will set even higher standards for increased thrust, reliability, flexibility, shorter lead-time and reduced costs. A challenge that perfectly suit our broad range of competences and ability to combine them for specific purposes that without doubt will be of benefit to other industry sectors.
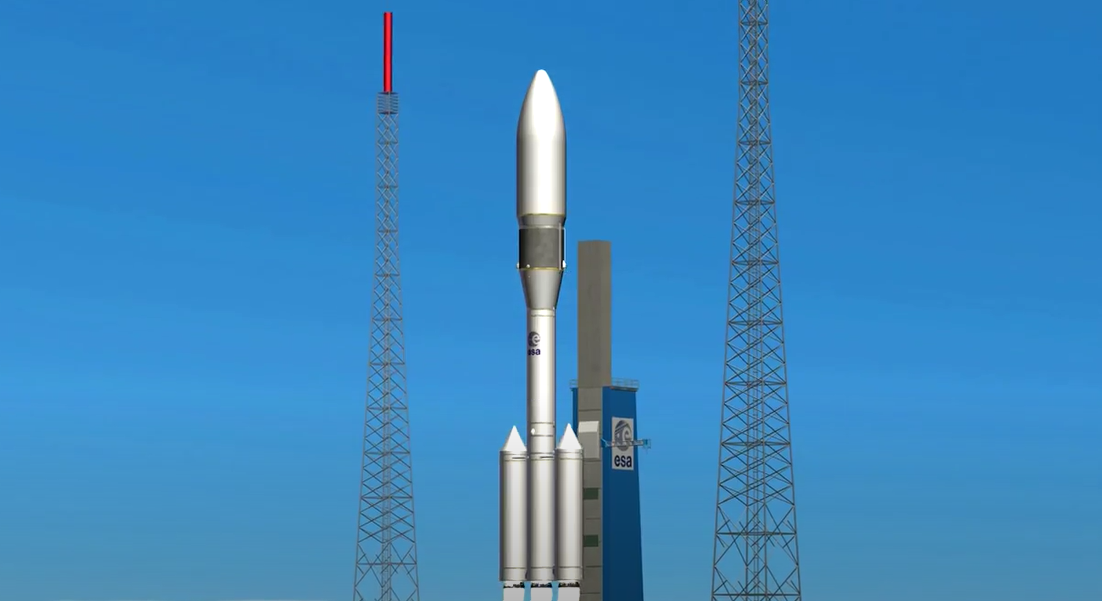
Laboratory and production facilities
At our headquarters near Copenhagen, Denmark, we have established laboratory and production facilities, equipped with state of the art equipment.
- lasers of different types and sizes; disk, Nd-YAG and CO2
- an automated and highly flexible weld cell, capable of handling up to 5 tons
- a unique Seamtracker for sandwich designs, using X-ray vision to guide the laser welding tool
- a broad range of X-ray and ultrasonic equipment, including a dedicated installation for automated inspection of full size nozzles.